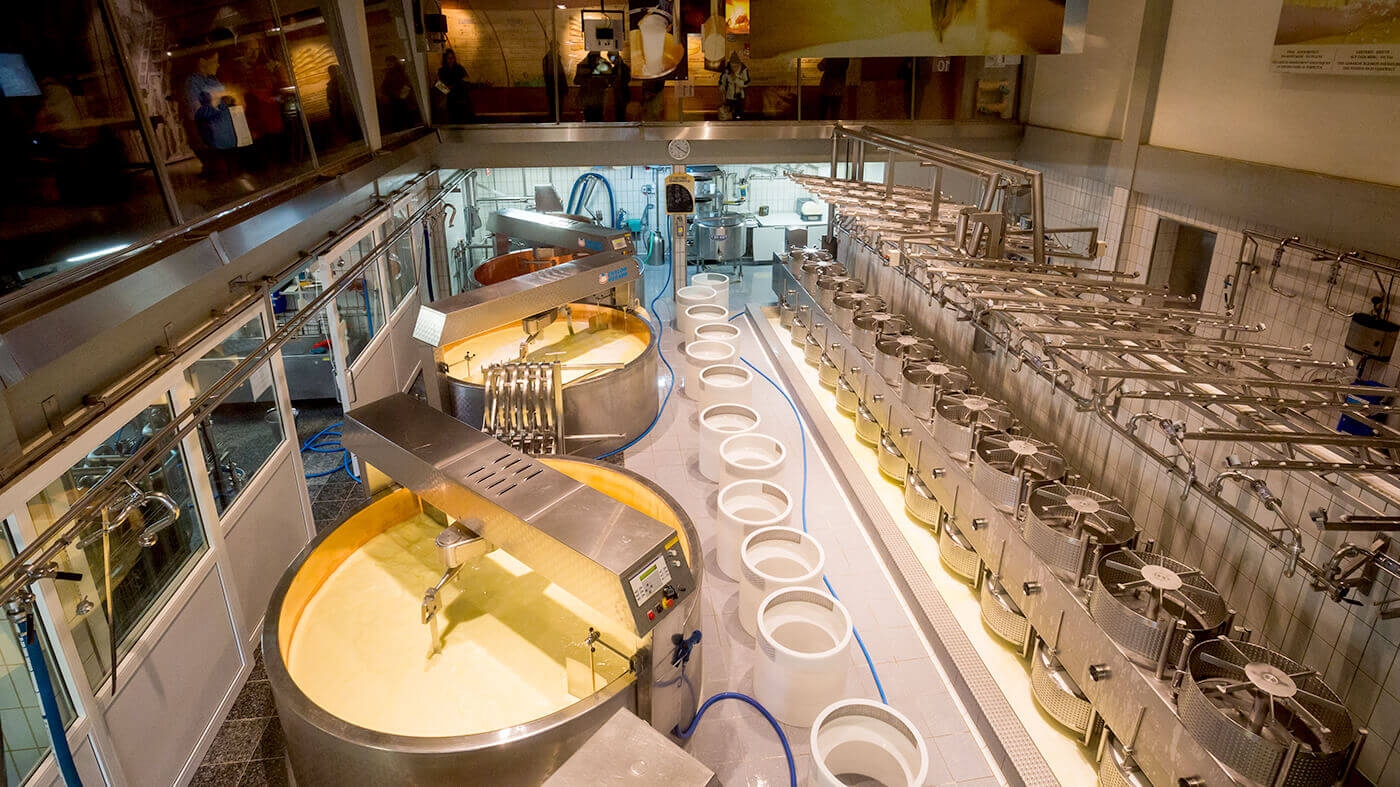
Avoid a cross-contamination nightmare with Dynamics Food
Reading time: 2 - 4 minutes
Without accuracy and safety at the heart of your Food company what do you have? A disaster waiting to happen.
Recently, we’ve seen Booths featuring in the Grocer in both February and May this year. They’ve had to recall corned beef and veg & soup mixes after they were found to be containing metal!
Obviously, Booths did the right thing and recalled all the product and issued statements apologising for any inconvenience. Although, it’s very unlikely that Booths will be on the phone to their supplier full of praise…
You don’t want to be the company responsible. A supermarket won’t be best impressed if the customers walking through their doors are exposed to a health risk thanks to the product you’ve sent to them.
Without reliable traceability you don’t have a leg to stand on
It’s incredibly rare that you will have to deal with a rogue nut falling off one of your machines, yet all Food manufacturers will have a metal detector at the end of their production line. If the nut somehow manages to get past your metal detector you need to be prepared to hit the recall button!
Straight off the bat, you will be aware that a product recall results in disruption to your operations whilst managing the recall. There is a direct cost associated with recalling stock, the activities associated with that and a risk of huge reputational damage. Loss of consumer confidence in your product could result in a significant long-term financial loss, so you need to be on top of any time your called into action for a recall.
Oh, so what do you do if you’ve been tracing your products using Excel? Well, enjoy scrolling through countless spreadsheets to see if you can track the relevant order and batch number. Yes, this is the same Excel spreadsheet that can be accessed by half of your company that everybody stares at and can’t say with a straight face that you’re all looking at one version of the truth.
If this is resonating at all, a bit of metal slipping into your supply chain is only the start of your problems! Food manufacturers typically produce in high volume and have a rapid inventory turnover, so using paper or Excel to track everything is only creating a headache that will debilitate your staff.
Dynamics Food will enable you to quickly identify all your raw material batches and the equipment used to manufacture your finished products. As a result, you can quickly respond to a customer audit – or in this case a product recall. Without farm-to-fork traceability you risk losing your BRC accreditation or even your entire business if you can’t deliver an accurate answer within the required time frame.
Implement strict zones to prevent a rogue allergen ordeal
Metal isn’t a very typical case that we see of a substance entering a supply chain, but let’s just say some rogue food falls in… maybe some peanuts?
Not to preach to the choir, but allergens and non-allergens and even smellier products like fish and cheese need to be kept apart so you aren’t presented with a contamination headache. Consumers purchase products with the faith they contain (x) to avoid allergens. If they unfortunately consume food contaminated with the allergen the consequences can be fatal.
Our end-to-end solution, Dynamics Food powered by Dynamics 365 Business Central will help you to implement strict zones and procedures to control allergens in your storage facilities to make it simpler for your team to stock the warehouse.
Dynamics Food can automatically generate clear labelling, directed put-away sequences and optimised bays and send all this information directly to handheld devices using our Clever Handheld for Warehousing App. In turn, you can quickly and safely put away your products.
To learn more about Dynamics Food, you can register your FREE ticket to our introductory seminar on Tuesday 2nd July from 9:30am to 12:30pm: ‘Boost your performance with a complete business software solution’.