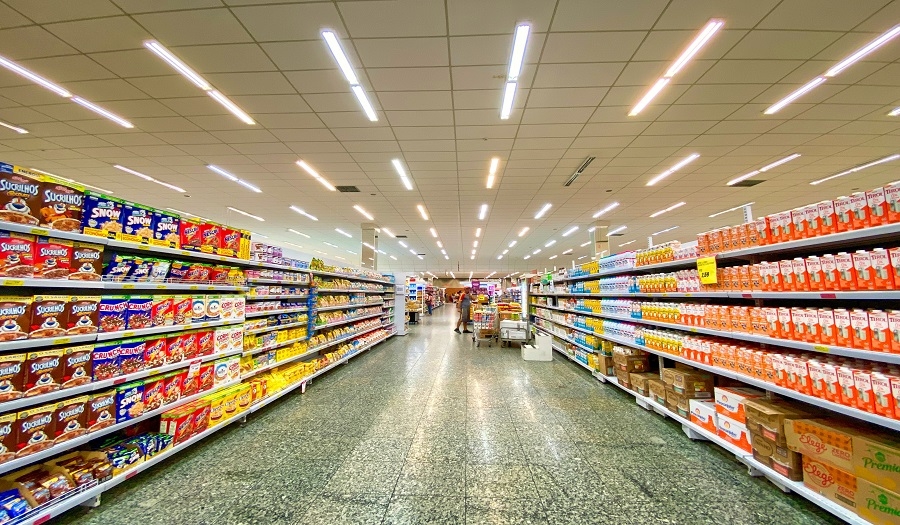
Why food businesses are struggling to keep up with spiralling UK food costs in 2025
Reading time: 2 - 3 minutes
Commodity-driven inflation is on the up, including wholesale meat, dairy, fruit, especially gooseberries (up 243%) and container costs from global trade disruptions are all major contributors (The Guardian). Forecasts suggest food inflation could reach 4.2% by late 2025 (The Food Foundation).
With everything from raw materials to transportation, energy and container costs going through the roof, the pressures and supply chain challenges have noticeably started to impact both the food industry and its customers.
Impact of spiralling food costs on consumers and retailers
Households are already responding. In 2025, families are choosing cheaper stores, with Aldi remaining Britain’s cheapest, followed closely by Lidl, meaning shoppers could save up to £70 per large shop (The Scottish Sun).
These pressures come as employers face rising national insurance, minimum wage, and new packaging tax, all eating into margins (Reuters). Retailers like Sainsbury’s warn that this may push prices even higher (The Times).
What rising costs mean for food businesses
Rising costs are a huge challenge for all food and drink businesses, with some producers capping the lines they typically sell to stay afloat. Businesses have been heavily impacted by so many factors that take constant and daily firefighting, with no end in sight.
Commodity supplies are not only hard to get hold of but are also increasing in price on an almost daily basis.
• Raw materials costs are volatile and climbing almost daily—some commodities have jumped over 58% since summer 2021.
• Labour shortages and skyrocketing logistics and energy bills put further strain on production, distribution, and storage.
• Regulatory changes, like packaging taxes and post-Brexit import rules, add complexity and cost to the supply chain.
How Dynamics Food equips you to respond to spiralling food costs
With the demand for energy, labour and transport placing significant pressures on just-in-time, cross-border supply chains that keep factories open and shelves stocked, real-time insight becomes essential.
Are you being flexible in where you are sourcing your stock? Are your distribution strategies as efficient as they can be? Could modernising your operations with full visibility and real-time data help you stay on top of your business, with no room to be left in the dark?
Here's how Dynamics Food, our ERP solution powered by Microsoft Dynamics 365 Business Central, keeps your business agile:
- Sourcing flexibility: Track cost shifts across suppliers and origins in real time.
- Distribution optimisation: Plan smarter routes and consolidate shipments to cut HGV and fuel spend.
- Operations visibility: Scan ingredients upon arrival, log every batch, and flag anomalies before they become costly defects.
- Traceability & waste control: Pinpoint inefficiencies in your production line and reduce waste through automated alerts.
- Data-led decisions: With a single dashboard view, spot cost breakout trends in energy, packaging, or labour, and act before margins erode.
All sectors in the food industry must embrace automation for better quality control, food safety, reduced waste, and more streamlined traceability.
Why now?
With food inflation currently at 3.7%–4.4% (May–June 2025), rising taxes, climate risk, and supply chain shocks, the status quo is fragile. Businesses using end-to-end ERP are better positioned to lower costs, win value-sensitive customers, and future-proof growth.