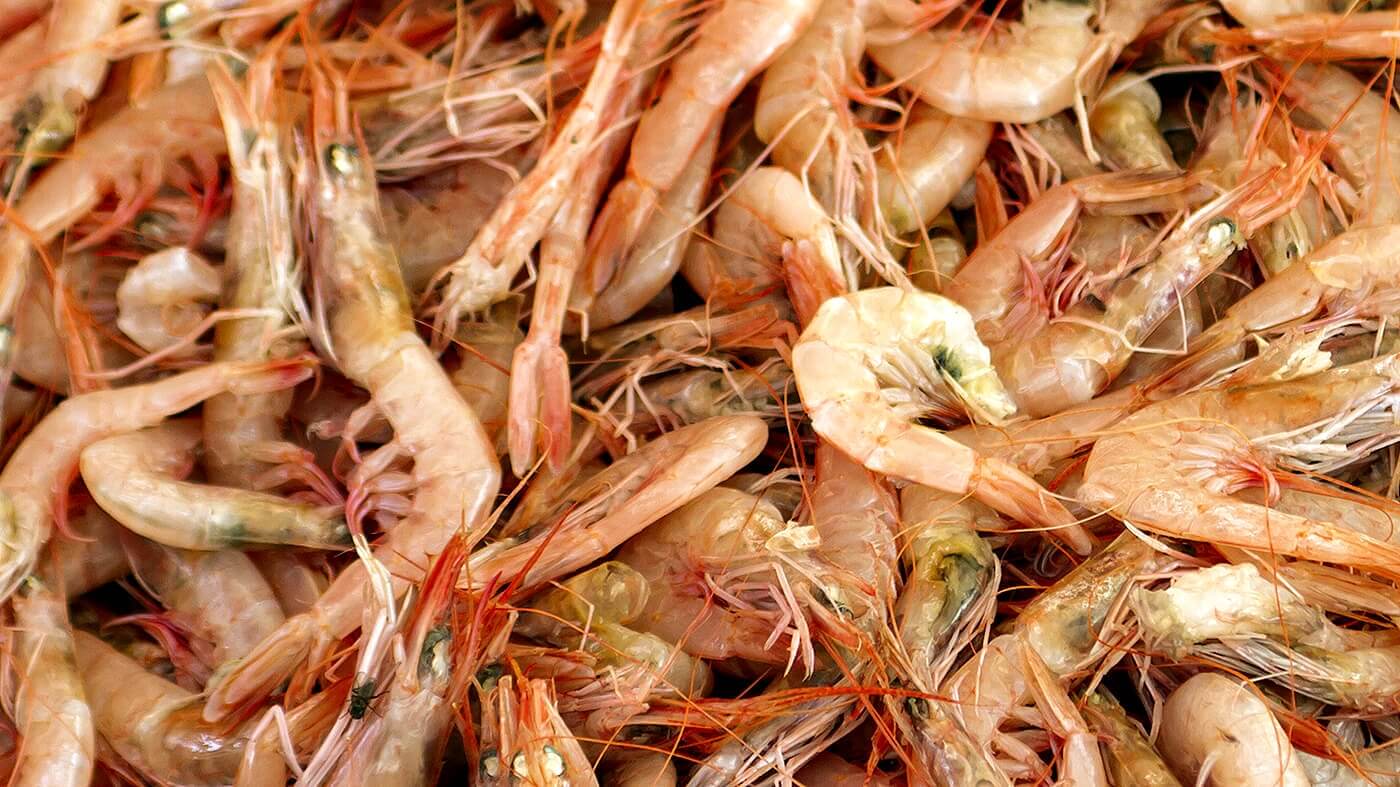
Tackle the challenges of Zoning and Cross-docking in the Food & Beverage Industry
Reading time: 2 - 3 minutes
In food warehouses, it’s essential to move quickly, or things can start to go bad… literally.
Getting product through the supply chain accurately and safely is crucial – or you will be haemorrhaging cash before products even leave the warehouse.
It’s more important than ever before to have sophisticated warehouse management in place to help regulate food safety, prevent cross-contamination and to manage shelf life and traceability.
In this two part blog series, we wanted to examine how companies can go the extra mile in Warehouse Management in the Food & Beverage Industry.
An end-to-end ERP business application, like Dynamics Food, can help manage every step products take through the warehouse and alleviate the many issues food manufacturers face in the warehouse…
Challenge 1: Zoning
Allergens and non-allergens, and even “smelly” products like fish and cheese, need to be kept apart to prevent cross-contamination.
This isn’t always the easiest thing to plan for in a warehouse, especially for food manufacturers where you could be storing a host of different produce at any one time.
Therefore, your warehouse needs to implement strict zones and procedures to control allergens in your storage facilities and make it easy for your team to stock the warehouse. Optimised bays, clear labelling and directed put-away sequences, automatically generated from your ERP system and provided directly to handheld devices, means products can be scanned and put-away quickly and safely.
Challenge 2: Cross-docking
If you are a food distributor, importer or exporter, you may receive perishable goods into the warehouse which need to be shipped, or part-shipped, straight back out of the door to retailers.
On one hand, this is great as it means that you don’t have to put away products to be picked again later, the customer will get the produce faster and there is minimal requirement for warehouse space.
However, this is does mean that you need to have “look ahead windows” i.e. visibility of what products, and when, need to be shipped back out again so you can control where products land in the warehouse to allow fast quality checks and ensure the least possible manual intervention.
An ERP system designed for the food industry can help you co-ordinate all the warehouse movements for inbound products from different vendors into a mixed pallet, which can then be delivered to the customer once the final item is received – and all in the most efficient way possible!
Attend our complimentary briefing: Boost performance with a single business software solution with Dynamics Food on either Tuesday 20th March from 10:00am-12:30pm in Wolverhampton, or alternatively Wednesday 9th May from 10:00am-12:30pm at Microsoft London.